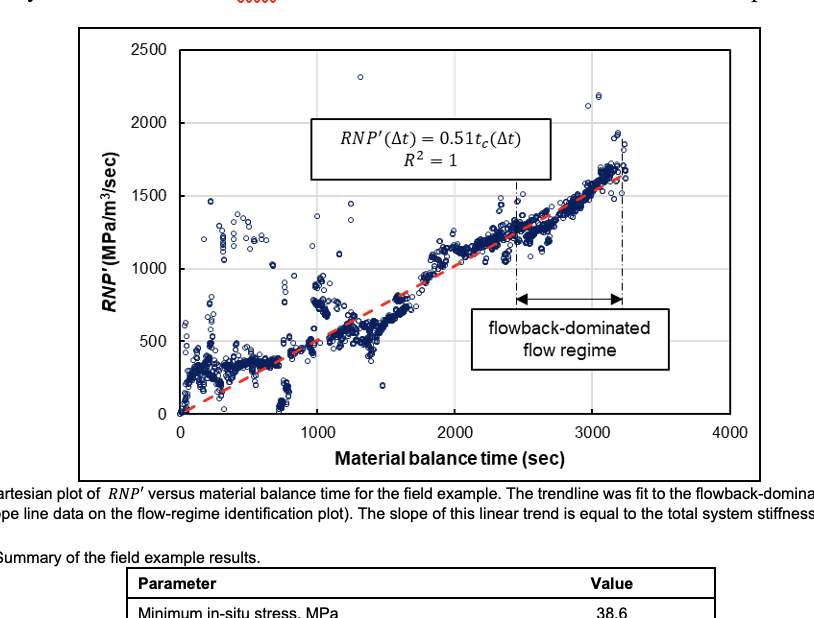
Estimating Reservoir Permeability and Fracture Surface Area Using the Flowback DFIT (DFIT-FBA)
The main parameters of interest derived from a diagnostic fracture injection test (DFIT) are minimum in-situ stress, reservoir pressure, and permeability. The latter two can only be obtained uniquely from the transient reservoir responses, often