Hydraulic fractures tend to propagate in a plane that is perpendicular to the least principal stress, as noted by Hubbert and Willis in 1957. As a result, unconventional oil and gas wells are typically drilled in the direction of Shmin to maximize drainage area. However, in some regions, due to acreage constrains by operators, wells are drilled in different directions, regardless of the stress orientation to maximize acreage production by maximizing the number of wells per acreage.
A recent study published by Rostami et al. (2020) evaluated the impact of well orientation on unconventional well productivity in the Bakken play. The authors analyzed 7198 wells showing the impact of well orientation on actual well first 24-months oil production per perforated foot (oil bbl/ft). The analysis demonstrated that the on-azimuth wells outperformed the off-azimuth wells in the Bakken play between 2007-2016, when wells were drilled using same size completion design and without depletion effects. The analysis showed that at low proppant loadings less than 600lb/ft, when most of wells were parent wells, there is a clear correlation between well orientation and well productivity, as shown in Fig. 1. However, with increasing the number of children wells, depletion and completion size increases of off-azimuth wells masked the impact of well orientation on well productivity, as shown in Fig. 2.


In this post, I investigate if well orientation is still significant for well productivity at higher proppant loadings when depletion does exist. Wells with different well orientations are simulated under same conditions (e.g., completion design size, zippering order, fluid type, proppant type, lateral length, well spacing, stage length, number of clusters, number of shots per cluster, no depletion, etc.) and production compared at 24-months. An example of on-azimuth versus off-azimuth drilling is illustrated in Fig.3.

(a) On-azimuth drilling, where wells are drilled in the direction of Shmin.
(b) Off-azimuth drilling, where wells are not drilled in the direction of Shmin.
Base case
I used the Bakken simulation template available in the latest ResFrac version. I simulate a three-well pad with 500ft well spacing in the Middle Bakken formation and drilled on-azimuth (in the direction of Shmin) as shown in Fig. 4.
The maximum principal stress (SHmax) direction in the Bakken shale is about N48◦E (Lund Snee and Zoback, 2020). Permeability is 400nd in the pay zone.
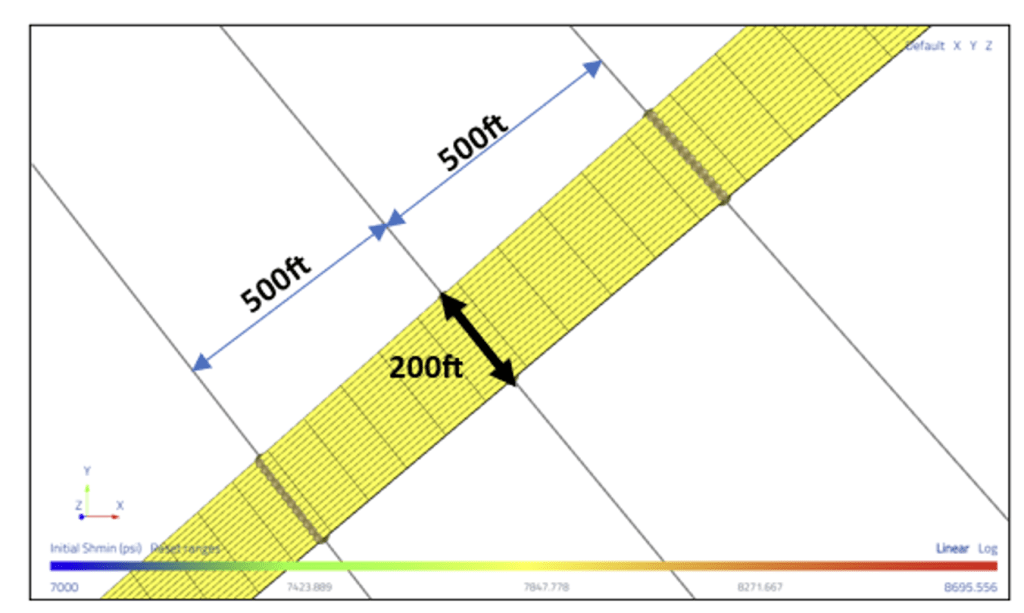
The base case is simulated with proppant loading of 200lb/ft, 25 bbl/ft, 100% 40/70 mesh proppant size, and a high viscosity friction reducer frac fluid, as shown in Fig. 5. One stage is simulated per well with a stage length of 200ft, 17ft cluster spacing, and two shots per cluster. An external frac with average fracture geometry is added for each well to mimic the stress shadowing from previous unmodeled stages.

Well orientation sensitivity analysis in ResFrac
One could duplicate the base case model and change well orientation manually. However, this approach is a time-consuming process and requires careful attention to maintaining the settings for each case. Instead, I created an automatic sensitivity analysis workflow by changing the SHmax direction in conjunction with changes to well orientation. This approach allows all cases to be generated automatically by ResFrac, with only a few minutes of setup.
I generated several off-azimuth cases using the automatic sensitivity analysis workflow by changing SHmax direction as shown below.
The first set of cases were generated using proppant loading of 200 lb/ft, the second set at 500 lb/ft, and the third set at 1000 lb/ft. Since the actual data shows a clear correlation between well orientation and well productivity at lower proppant concentrations, simulation sensitivity results trend at 200 lb/ft and 500 bb/ft are compared against actual data trend at same proppant loadings (based on the data reported by Rostami et al., in 2020), as shown in Fig. 6. The percentage change of production at 24 months of all off-azimuth cases is compared to the on-azimuth case production and plotted against well orientation. Based on the average SHmax direction in the Bakken play to be N48°E, wells with orientation between -50° and -30° to be on-azimuth (parallel to Shmin). The simulated cases at proppant loading of 200 and 500 lb/ft show a similar trend as of the actual data. The difference in the exact magnitudes can be attributed to differences in lateral length, fluid loading, cluster spacing, stage length, etc., but the trend is maintained.

The simulation of 1000 lb/ft shows a similar trend to the simulated 200 lb/ft and 500 lb/ft trends, as shown in Fig. 7. However, Rostami et al., show no correlation between well orientation and productivity in their analysis of 1000 lb/ft cases.
Rostami et al. posit the performance degradation was not seen in the data due to depletion effects as most of the 1000 lb/ft wells came later, and therefore more likely to offset depletion. A new set of simulated sensitivity analysis at 1000 lb/ft is used to investigate this hypothesis in the next section.

Although the lateral cluster spacing is the same for all tested cases as of 17ft, the off-azimuth cases show smaller fracture spacings due to changing well orientation that causes more stress shadowing and fracture anisotropy. Fig. 8 shows the on-azimuth case fracture propagation and pressure depletion profile after 30 years. The on-azimuth wells are drilled parallel to Shmin with a well orientation of -42◦. The on-azimuth wells have a stage length of 200ft and the fracture spacing is equal to the cluster spacing of 17ft. Fig. 9 shows one of the off-azimuth cases fracture propagation and pressure depletion profile after 30 years. The off-azimuth wells are not drilled parallel to Shmin, and the well orientation is 30◦. The off-azimuth wells have a stage length of 200ft with a cluster spacing of 17ft similar to the on-azimuth case, but the fracture spacing is only 5ft due to changing well orientation. The reduction in fracture spacing in the off-azimuth case results in a lower cluster efficiency of the entire 3wells pad with an average value of 58% compared to 94% cluster efficiency at the on-azimuth case.


New simulations
Depletion effect
A new base case was generated to investigate the effect of depletion on well orientation results. Three child wells are drilled on-azimuth after five years of depletion by a nearby parent well. The parent well is completed with 200lb/ft and 10 bbl/ft, where the child wells are completed with 1000 lb/ft and 25 bbl/ft. The results of the on-azimuth case with depletion are compared to the results of off-azimuth cases without depletion in Fig. 11.


When the on-azimuth wells (with well orientation of -42◦) are drilled after depletion, their productivity is lower than the off-azimuth wells that are drilled without depletion. These results confirm that depletion can mask the benefits of drilling wells on-azimuth wells.
Fig. 12 shows another set of simulation cases, where both on-azimuth and off-azimuth wells are drilled after depletion. When wells drilled after depletion, the effect of well orientation is lower compared to the cases without depletion.

Cluster spacing effect
New cases were generated with a wider cluster spacing of 50ft and compared to the base cases with 17ft using same stage length of 200ft. The results of the wider cluster spacing cases are shown in Fig. 13. Wider cluster spacing cases show a lesser effect of well orientation compared to the tighter cluster spacing cases.

Well spacing effect
New cases were generated with different well spacings of 300ft and 1000ft and compared to the base cases with 500ft. Wider well spacing cases show a lesser effect of well orientation compared to tighter well spacing cases as shown in Fig.14.

Conclusion
Drilling wells parallel to Shmin maximizes well productivity, as shown by actual and simulated well performance in the Bakken. However, the degree of production uplift cannot be fully attributed to well orientation. Above, I show that job size, depletion, cluster spacing, and well spacing all affect the impact of well orientation on performance. Actual well data need to be filtered based on many factors to get a representative impact of well orientation on productivity, such as well spacing, fluid loading, cluster spacing, stage length, frac fluid type, proppant type, zippering order, landing, etc. It is challenging to rigorously quantify the effect of well orientation versus completion design on well productivity in historical data. Simulation studies help to determine the impact of each parameter, helping operators optimize their development strategy. Simulation sensitivity analysis show that depletion, wider cluster spacing, and wider well spacing can lessen the effect of well orientation on well productivity.
References
Hubbert, M.K., and Willis, D.G. 1957. Mechanics of Hydraulic Fracturing. Transactions of Society of Petroleum Engineers of AIME, 210, 153-163.
Rostami, Erfan, Boness, Naomi, and Mark D. Zoback. “Significance of Well Orientation on Cumulative Production From Wells in the Bakken Region.” Paper presented at the SPE/AAPG/SEG Unconventional Resources Technology Conference, Virtual, July 2020. doi: https://doi.org/10.15530/urtec-2020-2813